Micro Sensors to Detect Shear Stress On Vascular Cells
1Department of Biomedical Engineering and Cardiovascular Medicine, University of Southern California,
Los Angeles, CA 90007 USA
2Department of Electrical Engineering, University of Southern California
This is an abstract
for a presentation given at the
11th
Foresight Conference on Molecular Nanotechnology
Introduction: Heart disease is the leading cause morbidity and mortality in the industrialized nations. Shear stress acting on the lumen surface of blood vessels intimately modulates the biological activities of vascular endothelial cells. We hereby develop shear-stress sensors at the dimension comparable to single cells by surface and bulk micro machining techniques. Our goal is to fabricate sensors for ex vivo or in vivo measurement of shear stress in the arterial circulation.
Methods: Based on the heat transfer principles, the sensors constitute the heating and heat-sensing element made of polysilicon material. The sensing element is lying on the diaphragm underneath which is a hollow cavity. This cavity reduces the heat transfer to the silicon substrate; thereby, increasing the sensitivity of the sensors. Constant temperature mode circuit was applied to drive the sensors. Micro shear stress sensors allow for the characterization of pulsatile flow profiles to the dynamic levels of vascular gene expression and signal transduction.
MicroSensor Fabrication: Nitride of 3000Å in thickness was first deposited by LPCVD on a 3-inch wafer. The pattern was developed and etched using RIE. KOH solution was used to etch off the silicon resulting in a cavity, after which two parallel slits were opened by RIE on the diaphragm to form connection between phosphrous doped polysilicon and the backside bonding. The wafer was then coated with polysilicon using LPCVD and doped with phosphorus at 1016 cm_ at 40KeV, followed by aluminum metallization on the back side.The final step was to remove the excess polysilicon to establish precise dimensions of the sensing element at 80 × 2 × 3 µm.
Figure 1. Flow Process
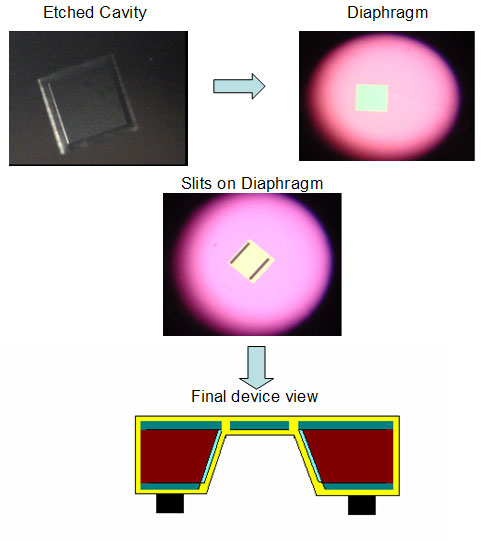
Final Goal: To integrate the shear stress sensor into pulsatile flow model to study the effects of real-time shear stress on the dynamics of endothelial gene expression and function.
References:
[1] F. Jiang, Y. Xu, T. Weng, Z. Han, Y.-C. Tai, A. Huang, C.-M. Ho, and S. Newbern, "Flexible shear stress sensor skin for aerodynamics applications," presented at MEMS 2000 Miyazaki,Japan2000.
[2] Parylene Data Sheet, Specialty Coating System, Indianapolis.
[3] X. Q. Wang, X. Yang, K. Walsh, and Y.-C. Tai, "Gas-phase silicon etching with bromine trifluoride," presented at Tranducers 97. Chicago, IL, USA, 1997.
[4] Tzung K Hsiai,Sung K Cho,Henry M.Honda, Susan Hama, Mohamad Navab,Linda
[5] Huang, Ho et al.1995. Equations.
Abstract in Microsoft Word® format 150,854 bytes
*Corresponding Address:
Tzung K. Hsiai
Department of Biomedical Engineering and Cardiovascular Medicine
University of Southern California
3650 McClintock Ave, University Park, OHE 500
Los Angeles, CA 90007 USA
Phone: 213-804-8308 Fax: 213-740-0343
Email: [email protected]
Web: http://www.usc.edu/dept/biomed/facpages/hsiai.php?cat=faculty
|