Simulation and Experiments on Friction and Wear of Diamond: A
material for MEMS and NEMS applications
by
Tahir Cagin*,a,
Jianwei Chea, Michael N. Gardosb,
Amir Fijanyc, and William A. Goddard, IIIa
a
Materials and Process Simulation Center,
California Institute of Technology,
Pasadena, CA, 91125
bRaytheon, El Segundo, California, 90245
cJet Propulsion Laboratory, NASA, Pasadena,
CA
*Web page: http://www.wag.caltech.edu/home/tahir/
This is a draft paper for the
Sixth
Foresight Conference on Molecular Nanotechnology.
The final version has been submitted
for publication in the special Conference issue of Nanotechnology.
Abstract
To date most of the microelectromechanical system (MEMS) devices[1-7]
have been based on Silicon. This is due to the technological knowhow
accumulated on manipulating, machining, manufacturing of Silicon.
However, only very few devices involve moving parts. This is because of
the rapid wear arising from high friction in these Silicon based systems.
Recent tribometric experiments carried out by Gardos on Silicon and
polycrystalline diamond (PCD) [8-14] show that this rapid
wear is caused by a variety of factors, related both to surface chemistry and
cohesive energy density of these likely MEMS bearing materials. In particular, the 1.8-times
strength of the C-C bond in diamond as opposed to the Si-Si bond in the bulk
translates into more than 104-times difference in wear rates, even
though the difference in flexural strength is only 20-times, in hardness
10-times and the fracture toughness 5-times. It also has been shown that the
wear rates of Silicon and PCD are controlled by high-friction-induced surface
cracking, and the friction is controlled by the number of dangling,
reconstructed or adsorbate-passivated surface bonds. Therefore, theoretical
and tribological characterization of Si and PCD surfaces is essential prior to
device fabrication to assure reliable MEMS operation unded various atmospheric
environments, especially at elevated temperatures.
As a part of rational design and manufacturing of MEMS devices containing
moving mechanical assemblies (MEMS-MMA) and especially
nanoelecctromechanical devices (NEMS), the theory and simulation could play
an improtant role. Predicting materials properties such as friction, wear,
thermal conductivity is of critical importance for materials and components to
be used in MEMS-MMAs.
In this paper, we present theoretical studies of friction and wear
processes on diamond surfaces using a steady state Molecular Dynamics Method.
We studied the atomic friction of the diamond (100)-surface using an extended
bond-order-dependent potential for hydrocarbon systems. Unlike traditional
empirical potentials, bond order potentials can simulate bond breaking and
formation processes. Therefore, it is a natural choice to study surface
dynamics under friction and wear. In order to calculate the material properties
correctly, we have established a consistent approach to incorporate non-bond
interactions into the bond order potentials. We have also developed an
easy-to-use software to evaluate the atomic-level friction
coefficient for an arbitrary system, and interfaced it into a third party
graphical software.
Introduction
Microelectromechanical Systems (MEMS) is an emerging enabling technology that
merges advances in information processing, storage, and display with advances
in sensors and actuators to bring about a revolution in the way we perceive
and control the environment [1-7].
MEMS is a natural progression in the capabilities of semiconductor devices.
The ability of MEMS to gather and process information, decide on a course
of action, and control the environment through actuators increases the
affordability, functionality, and number of smart systems.
A very significant role is attributed to MEMS for
the technologies of 21st century, as applied to the following areas:
- Optical Switches and Aligners
- Parts handling in manufacturing
- Inertial Navigation
- Pumps and Valves
- Data Storage
- Computer Display
- Structural Control of Aircrafts
The design of MEMS presents challenges at various length and time scales. The length scale ranges from Angstroms to millimeters where theories such as quantum mechanics, classical mechanics, solid (continuum) mechanics may be employed to improve practical performance.
Most of the MEMS devices explored and designed to date are based on Silicon, due to technological know-how accumulated on this particular semiconductor on manipulating, machining, manufacturing etc. on the microscale. Recent tribometric experiments carried out at Hughes by Gardos [8-11] strengthen the hypothesis in that the magnitude of adhesion and thus the adhesive friction between silicon and diamond surfaces are essentially defined by the number of dangling (high-friction), reconstructed (reduced-friction) or adsorbate-passivated (low-friction) surface bonds. Incipient linking of the sliding counterfaces by unsaturated (dangling) bonds on heating and their passivation by benign, chemi-sorbed gasses (e.g., hydrogen) were suggested as the primary causes of radically increased and reduced adhesion and friction, respectively. Hence to a performance degradation in Silicon based MEMS through a higher sliding friction and a resulting short wear life for devices with moving parts.
With this observation one must look into alternative materials, such as single crystal and polycrystalline diamond where sliding friction measurements lead to considerably lower values. As previously mentioned the wear rate of PCD is about four orders of magnitude lower than those of variety of Si crystallinites (poly-Si, Si(100) and Si(111)). In designing the next generation MEMS using PCD, there is a lot to be done. The hypothesis brought forth by Gardos to explain his experimental results on the basis of the chemical state of the surface bonds needs to be explored and rationalized theoretically.
Replacing conventional devices with their MEMS/NEMS analogs presents both opportunities and challanges. The evolution of small machines and sensors demonstrates that ever-increasing number of these devices with electronic circuits will yield a window to the world of motion, sound, heat and other physical forces. The current MEMS devices contain about 10 components MEMS devices. The anticipated applications such as pumps and valves require 103 - 105 components, optical aligners may have 102 - 104 components. In computer displays this range goes upto 106 or 107. The design, processing and fabrication methodology for such applications require research not only in the materials area but also on the operational conditions of such multi components systems, where simulation codes developed for robotics application will play a critical role [15]. Simulation of systems with such large number of components will require the use of highly optimized parallel programs which we aim at developing and testing through MEMS applications.
![[microgear]](microgear.jpg)
Figure 1. A PCD proto-microgear grown on a Si wafer (from Dr. K. V. Ravi, Lockheed R&D).
Problem of Friction and Wear
Friction is an unavoidable, parasitic force in flea-powered MEMS-MMA's. It is a crucial factor that determines not only efficiency but durability. Gardos' SEM-tribometric data in [8-13] indicated that high adhesive friction within the Hertzian contact zones of both Silicon and PCD causes shear-induced microcracking in the wake of the rolling/sliding contact. The ensuing wear and tolerance losses alone will fail these devices, especially when they are fabricated from high friction and high wear rate bearing materials such as Silicon. Although the hardness and chemical stability of PCD renders it a difficult material to shape into MEMS-MMA components and assembly of these components into complex micromachinery is even more difficult than those made of Silicon, the properties of PCD are far better for MEMS-MMA applications. Diamond is the hardest material known in nature, with a surprisingly high strength and fracture toughness in its polycrystalline form. Its thermal conductivity is high, readily dissipating both frictional and microelectronics-generated heat from functional areas. Due to the higher strength of the covalent carbon-hydrogen bonds, as compared to that of the silicon-hydrogen bonds, hydride-passivated PCD surfaces remain lubricative at higher operating temperatures.
![[wear scars in Si(100)]](si100wear.gif)
Figure 2. Wear scars on a Si(100) surface.
It is important to understand that bench-level testing in the laboratory is useful only if the behavior of real devices is closely approximated. Theory becomes a problem-solving tool only if it accurately mimics practice. For example, the high friction and rapid wear of a Silicon rotor in an electrostatic micromotor is better approximated by SEM tribometry under realistic Hertzian stresses than by the action of a sharp atomic force microscope (AFM) Silicon (wearless) tip brought only close to a highly flat Silicon surface. Employing the concept of a reactive hydrocarbon potential, the molecular dynamics simulation technique described in the present paper is able to study both the "wearless" (AFM-measured) friction forces at the atomic level, as well as the coefficients of friction (COF) measured under full Hertzian (engineering) contact conditions. As an added benefit, the reactive potential permits the study of lubricative surface adsorbates. Therefore, simulation of MEMS-MMA interfaces can not only rationalize tribometric results, but provide detailed infor-mation on contact kinematics under artificially- induced surface chemical conditions. The various likely fabrication processes can also be iterated before bench-level experiments are attempted.
Experiments
The SEM Tribometer and Test Procedures
As shown schematically in Figure 3, a small flat is oscillated against a hemispherically tipped and dead-weight-loaded pin, either in the ~1.33x10 -3 Pa (~1 x 10 -5 Torr) vacuum of the SEM column or in a lidded and preferentially pumped Knudsen cell-like subchamber backfilled and continually purged with selected, high purity gases (e.g., air, H2, He, N2 and O2) introduced from lecture bottles.
![[SEM Tribometer]](semtribo.jpg)
Figure 3. The schematic of the SEM tribometer.
The stage housing the heated flat is oscillated at 0.5 Hz, with a small average sliding speed of 3.5 mm/s. The Hertzian contact stresses are applied by normal (dead weight) loads on the pin, ranging from 6 to 50 g (0.06 to 0.49 N). The flat may be held at room temperature or heated and cooled to and from 1100°C (max.) at various thermal ramping rates. The friction forces are archived and converted in real time to averaged coefficients of friction (COF) by a desktop computer, using commercial data logging and analysis software. A more thorough description of the apparatus and procedures for examining PCD and Si in vacuum may be found in [14]. The equivalent methods for testing a variety of materials in partial pressures of H2 and O2 were previously described in [8,9] and [11], respectively. A constantly exchanged gas environment maintained at a given partial pressure offers several benefits to testing PCD. Several thermally ramped experiments could be repeated without breaking either the SEM column vacuum or the particular test atmosphere, because the extremely low wear of diamond precluded the need to photograph the wear scars after each test. Further-more, the high thermal conductivity of the gasses (as compared to vacuum) allows cooling of the friction force strain gages to near RT in a reasonably short period of time between tests.
The SEM tribometer has no in-situ surface analytical capability. Nevertheless, the extensive Si and PCD work by Gardos in [8-12] and related data from the literature has allowed some interpretation of the friction trends as a function of temperature and atmosphere in terms of atomic-level surface behavior. The magnitude of adhesion and thus the shape and magnitude of the SEM-tribometric COF curves in were defined by the number of dangling (high-friction), recon-structed (reduced-friction) or adsorbate-passivated (low-friction) surface bonds. Incipient linking of the sliding counterfaces by unsaturated bonds on heating and their deactivation by benign adsorbates on cooling were suggested as the primary causes of radically increased and reduced adhesion and friction, respectively.
Even if the SEM tribometer had in situ surface analytical capability or the analyses of the wear scars were attempted after the experiments in vacuum and partial pressures of hydrogen, commonly employed techniques such as Auger electron spectroscopy (AES) and X-ray photoelec-tron spectroscopy (XPS) are not sensitive to surface hydrides. Infrared spectroscopy is able to show hydrogen, oxygen or hydroxyl moieties covalently bonded to carbon, but lacks sensitivity for an essentially monolayer coverage (or less in case of surface reconstruction). Electron energy loss spectroscopies require conductive samples of high surface finish to avoid charging effects and increase electron reflectivity at low electron energies. Since wear scars are still rough on the microscopic scale and any exposure to atmospheric air leads to some contamination with adventitious carbon, this analytical technique becomes problematic with tribospecimens. Surface charging is higher with increased purity (i.e., progressively lower sp2 content) and causes shifts in the AES and XPS energy peaks. Where the wear scar is much smaller than the diameter of the probing XPS beam, the chemical state of the worn surface cannot be determined with certainty.
As a consequence, explaining any kind of interaction at the atomic level via macroscopic friction measurements could only be validated by testing a large number of Si and PCD crystal structures with the highest possible crystallographic and environ-mental control in vacuum and in partial pressures of hydrogen, and watching for any changes in the characteristic friction and wear trends. To date, the results and the related literature data helped explain the high torque and wear rate of miniaturized tribomechanical parts made from Si, why molecular hydrogen can act as an atomic level lubricant for both Si and PCD, and why PCD is a better bearing material for dynamic MEMS-MMA's than Si.
SEM-Tribometric Results
As more thoroughly described by Gardos in [8-14], typical SEM-tribometric coefficient of friction (COF) trends with PCD and Silicon interfaces heated and cooled in vacuum and hydrogen are exeplified by the unusual, "rabbit-ear-like" friction curves shown in Figure 4. These typical COF functions contain a great deal of conjectured surface chemical information , but are yet to be confirmed by independent experimentation or rationalized by theoretical simulation.
Figure 4. Friction profile for two different tracks display "rabbit-ear-like" curves.
As depicted in Figure 4, the substantial increase in COF PCD and COF Si at some elevated temperature is attributed to the generation of danglig surface bonds on the desorption of adsorbates combined with wear-induced tearing of the counterfaces. There is a shift in the COF-increase peaks to higher temperatures going from vacuum to low partial pressures of hydrogen test atmospheres. This shift is in accordance with the LeChâtelier Principle: if a reaction (the desorption of an adsorbate) results in a gas (e.g., H2) as a product, increasing the partial pressure (activity) of this gas in the tribometer chamber will retard the reaction, i.e., desorption will occur at higher temperatures [9].
The substantial reduction in the COF PCD on cooling in vacuum or in hydrogen is the foot-print of tribocatalytically enhanced chemisorption of water (i.e., the residual atmospheric moisture in the SEM column) or molecular hydrogen purposely introduced into the test chamber. There is also some reduction in the COF Si in vacuum on cooling, attributed to the chemisorption of residual water vapor in the SEM column. However, the final friction values near room temperature were not as low as the starting COF, as explained by the large increase in the real and apparent areas of contact resulting from the high wear rate of Si (some 104-times greater than those of PCD).
In contrast, the final COF Si in hydrogen at room temperature was consistently and signi- ficantly higher than in vacuum. Although this different trend is consistent with the lack of activa-tion energy for the chemisorption of H2 on cooling [9], it is difficult to believe that surface bonds remain unsaturated at or near room temperature in the presence of hydrogen. If this pheno-menon is not caused by unpassivated free radicals but by the interaction of variously reconstructed surfaces with energies changing as a function of temperature in the presence of adsorbates [Reference], the SEM tribometer is not able to separate these variables. The trough-like "bathtub" (dip-and-rise) curve in the COF at the highest temperatures, both in vacuum and in rarefied hydrogen, can be attributed to surface re(de)construction. Continued heating of the progressively degassed and worn surfaces reconstructs the dangling bonds to reduce the surface energy, apparently unhindered by the ongoing tribological action. Since the worn and crystallographically always miscut surfaces display crystallographic disorder, a variety of recon-struction cells can be formed. However, the real area of contact is still extremely large relative to pi-chain dimensions. It follows, therefore, that a global reduction in COF may be explained by a local decrease in the surface energy within each nanoscaled reconstruction mosaic.
Once the heating stops and the rubbed surfaces cool below a certain temperature, the activation energy needed to keep the bonds reconstructed is lost. There is a significant rise in friction from the deepest part of the COF trough due to regeneration of the dangling bonds (deconstruction), commensurate with an increase in surface energy (another COF peak). As the contact is cooled further to the temperature where adsorbates readily chemisorb and passivate the deconstructed surface bonds, the lowest possible surface energy and a large reduction in COF are attained.
The details of this typical friction trend characteristic to both PCD and the silicon crystal structures [e.g., poly-Si, Si(100) and Si(111)] tested lend themselved well to theoretical treatment by ab-initio [19] and molecular dynamics calculations.
Theoretical Background
Molecular dynamics have been widely used to study structures and properties of variety substance. It provides the information on atomic level directly. Therefore, people can test their theories, explain the experimental results on the bases of atomic motion. In molecular dynamics simulation, one of the most important steps is to apply a proper empirical potential to the system of interest. For a system with a given initial condition, its subsequent dynamics are completely determined by the potential surface that it evolves on. Choosing a proper classical potential is crucial to reproduce the real physical behavior of the system.
Usually, friction is always accompanied by wear. Although it is possible to have wearless friction at atomic level, we would like to have a potential which is applicable under both conditions for consistence. In our study, we employ a modified bond order hydrocarbon potential [16-18]. It allows chemical reactions during dynamics, therefore, it is a natural candidate to simulate both wearless friction and general friction. Our modified Brenner bond order potential energy is written as,
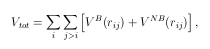
where
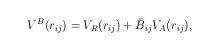

In above equations, VB is a bond term, VNB is a nonbond term. VR and VA are the repulsive and attractive portion of a general Morse potential, respectively. Bij is the bond order parameter. In above equations P(i,j) is a screening function which considers the nonbond contribution properly. VLR is a general notation for nonbond interaction, such as van de Waals or Coulomb forces.
Simulation Results
With the modified bond order potential, we study the friction process on reconstructed diamond 100 surfaces. Both bare and hydrogenated surfaces are investigated. In our simulation, two diamond crystals are put in contact. The bottom two layers of the lower block are held still, a constant velocity is assigned to the top two layers of the upper block. The external forces that are required to maintain the steady motion are recorded. As a result, the ratio between the external driving force and the normal force gives the friction coefficient. In order to prevent the system from being heated up, a stochastic thermal bath has been applied to maintain the average kinetic energy.
![[Fig 5]](frictionfig1.gif)
Figure 5. The top view of Hydrogenated 100 surfaces of two diamond crystal. Only the atoms at the interface are shown here. The gray and blue atoms are carbon atoms of moving block and fixed block, respectively. The red and green atoms are hydrogen atoms of upper and lower surfaces, respectively.
In Fig. 5, we show the top view of two hydrogenated diamond 100 surfaces. Both surfaces are C 2 x 1 reconstructed. However, they are placed 90o respect to each other. The atoms on each surface create the surface potential with mountains and valleys. One can expect that different friction forces might arise from different movement on the microscopic level. The general experimental friction coefficients are the average value of many different microscopic results. In particular, the friction of poly crystalline diamond (PCD) is an average quantity of friction along many different crystal orientation. In our simulation, we are able to extract each individual friction coefficient for each direction on a specific surface. We call it differential friction coefficient. For the system shown in Fig. 5, we have calculated the differential friction for three different sliding directions. The three characteristic directions are x-direction, y-direction, and xy-direction. Obviously, sliding along xy-direction will have lowest resistance, because the path is lying along a potential valley. On the other hand, moving in the x-direction and y-direction has to climb up the potential barriers created by the presence of hydrogen atoms along the sliding direction.
![[Fig 6]](frictionfig2.gif)
Figure 6. Running average of normal forces. The force from x-direction movement is shown as solid line, the force from y-direction movement is shown as dash line, and the force from xy-direction movement is shown as dotted line.
In Fig. 6, we show the running averages of forces in the normal direction respect to the movement. The initial oscillations represent the process of reaching a steady state motion. Usually, the system arrives at the steady state within 10 ps. The constant velocity is maintained at 1 A/ps (100 m/s). Fig. 6 illustrates that the normal forces are very similar despite different moving directions. This result indicates that any difference in the differential friction coefficients can only come from different motion arrangements in the regime of our investigation. Our normal force is around 850 kcal/A/mol. Fig. 7 depicts the running average of the friction coefficients calculated for each sliding direction. As we expected, xy-direction has lowest friction coefficient, and x-direction and y-direction have high friction coefficients. If the two surfaces are perfectly aligned, x-direction and y-direction would have same friction coefficient. However, in our simulation, the model set up such that the top block is shifted in y-direction, to create a slightly different potential energy surface. In turn, this gives rise to smaller friction coefficient along x-direction.
![[Fig 7]](frictionfig3.gif)
Figure 7. Running average of differential friction coefficients. The solid line shows x-direction friction coefficient, the dash line shows y-direction friction coefficient, and the dotted line shows xy-direction friction coefficient.
One phenomenon that always accompanied with friction is energy dissipation. The friction coefficient can also be extracted from energy consumption curve. In Fig. 8, we plot the external work done to the system as a function of time. The slope of each curve gives the friction coefficient, and the detailed features of each curve reflects the potential surface contour along the each slide path. For instance, the three peaks in each period of xy-direction curve represent each hydrogen atom on the lower surface passing through three reconstructed C--C bonds of the upper surface.
![[Fig 8]](frictionfig4.gif)
Figure 8. External work done to the system as a function of time. The solid line is calculated from x-direction motion, the dash line is calculated from x-direction motion, the dash line is calculated from y-direction motion, and the dotted line is calculated from xy-direction motion.
In general, clean crystal surfaces are less stable because of the dangling bonds. This is also the case for diamond. The pi-chain reconstructed diamond (100) surface is known to be energetically favorable. However, when two such surfaces are brought together, they can easily react, which increases the friction force more than 2 orders of magnitude. In this case, frictional force comes from not only nonbond interaction, but chemical binding forces. This is the main cause of large frictional force. Fig. 9 shows the running average of the friction coefficient and the external work done on the system. Compared to the hydrogenated surface, the friction coefficient is much larger. Our simulation reveals the cost of formation and breaking of chemical bonds on the interface during structures of our simulation are displayed in Fig. 10.
![[Fig 9]](frictionfig5.gif)
Figure 9. The running average of a differential friction coefficient and external work as a function of time.
![[Fig 10]](frictionfig6.gif)
Figure 10. The initial and final structures of two diamond crystals sliding respect to each other. The red and blue atoms represent the surface atoms.
Conclusions and Discussions
Friction and wear are complicated physical and chemical processes. Our investigation mainly focused on atomic scale origin of friction. For crystal surfaces, sliding in different directions gives different friction coefficients. The surface potential energy landscape (which is periodic for single crystal diamond) is the main source of this. Also, dangling bonds on surfaces can create large frictional force. In this case, it is necessary to break these bond in order to have relative movement. Our calculations clearly show how these aspects contribute to the atomic friction and wear. In all cases, surface passivation has to be done to have small friction and wear rate. If possible, a specific sliding direction is preferred. Another way of decreasing friction forces is to add proper lubricants to the interface. Gardos[11] has reported that water is a perfect lubricant for both diamond and silicon. It also needs to be noted that there are other factors giving rise to overall frictional force. For instance, surface asperities and contact area can dramatically modify total friction coefficients.
The modified bond order potential is capable of dealing both wearless friction and general friction. For this theoretical study, we have developed an easy-to-use software that can calculate the friction coefficient for a given system [20] and interfaced to a graphical molecular modeling package [21] usink SDK [22]. This program can also simulate the frictional process between various type of surfaces (lubricated or not). It can be used by experimenters, as a guidance in optimizing lubricants and study the behavior of these lubricant. This is extremely important for designing and further modification of a new mechanical system and lubricants.
Acknowledgments
This research was funded by a grant from NASA on computationala nanotechnology.
Dr. MN Gardos acknowledges funding from AFOSR tribology program. The
facilities of the MSC are also supported by grants from NSF (ASC 92-17368 and
CHE 91-12279), ARO (MURI), ARO (DURIP), ONR (DURIP), Chevron Petroleum
Technology Co., Asahi Chemical, Owens-Corning, Exxon, Chevron Chemical Co.,
Asahi Glass, Chevron Research Technology Co., Avery Dennison, BP America, and
Beckman Institute.
References
- Engineering Microscopic Machines, by Ken Gabriel,
Scientific American, Sept. 1995, Vol. 273, No. 3, pp. 118-121.
- Silicon micromechanics: sensors and actuators on a chip,
by Roger T. Howe, Richard S. Muller, Kaigham J. Gabriel, William S. N. Trimmer.
IEEE Spectrum, July 1990.
- Fabrication Technology for an Integrated Surface-Micromachined Sensor,
by Theresa A. Core, W. K. Tsang, Steven J. Sherman.
Solid State Technology, October 1993.
- Micro-machines hold promise for aerospace, by William B. Scott.
Aviation Week and Space Technology, March 1993.
- Mighty Mites Hit it Big, by Peter Coy, John Carey, and Nei Gross.
Business Week, April 1993.
- Micron Machinations, by Gary Stix. Scientific American, November 1992.
- Mirrors on a Chip, by Jack M. Younse. IEEE Spectrum, November 1993.
- M. N. Gardos (1996) Trib. Lett. Volume 2, pages 173-187, Surface
chemistry-controlled tribological behavior of Si and diamond.
- M.N. Gardos, Tribol. Lett. 2 (1996) 355.
- M. N. Gardos (1998) Trib. Lett. Volume 4, pages 175-188,
Re(de)construction-induced friction signatures of polished polycrystalline diamond
films in vacuum and Hydrogen
- M.N. Gardos, in "Protective Coatings and Thin Films," Proc. NATO Adv. Res.
Workshop, May 30 - June 5, 1996, NATO ARW Series, eds. Y. Pauleau and P.B.
Barna, (Kluwer Academic Publishers, Dordrecht, The Netherlands, 1997), p.185.
- M.N. Gardos and B.L.Soriano, J. Mater. Res. 5 (1990) 2599.
- M.N. Gardos, in Synthetic Diamond: Emerging CVD Science and Technology,
Electrochem. Soc. Monograph, eds. K.E. Spear, and J.P. Dismukes (Wiley, New
York, 1994), ch. 12, p. 419.
- M.N. Gardos and K.V. Ravi, Dia. Films & Technol. 4, (1994) 139.
(1993) 674.
- A. Fijany, T. Cagin, A. J. Botero, and W. A. Goddard, III. "Novel Algorithms for
massively parallel, long term simulation of molecular dynamics systems," Advances in
Engineering Software, 29, 441-450 (1998).
- D. W. Brenner, ``Empirical potential for hydrocarbons for use in
simulating the chemical vapor deposition of diamond films,'' Phys. Rev. B
42, 9458 (1990).
- J. Che, T. Cagin, and W. A. Goddard, III,
Extenion of Bond Order Dependent Potentials to include Long Range Interactions
Theochim. Act. (in press).
- J. Che, T. Cagin, and W. A. Goddard, III, "Studies of Fullerenes and Carbon
Nanotubes by an Extended Bond Order Potential" this conference.
- S. P. Walch, W. A. Goddard III, and T. Cagin "Computational Studies of the
Interaction of H/H2 with Diamond and Silicon Surfaces", this conference.
- T. Cagin and J. Che, Steady State Molecular Dynamics, 1998
- Cerius2 from Molecular Simulations Inc., San Diego, CA.
- Cerius2 Software Developers Kit (SDK), 1998, from Molecular
Simulations Inc., San Diego, CA.
|