Optimal Tracking of Piezo-based Nano-positioners
by
D. Crofta, S. Stilsonb , S. Devasia
*
Mechanical Engineering Department
University of Utah, Salt Lake City, UT 84112
*Corresponding author: [email protected]
Web page: http://www.mech.utah.edu/~santosh
a[email protected]
b[email protected]
Work Supported by NSF Grant DMI 9612300
This is a draft paper for the
Sixth
Foresight Conference on Molecular Nanotechnology.
This paper is also available on the author's Web site at: http://www.mech.utah.edu/~croft/nanotech/nano.html.
The final version will be submitted
for publication in the special Conference issue of Nanotechnology.
Abstract
This paper addresses the optimal tracking of piezo-positioners, which are fundamental tools used in high precision positioning for nanotechnology applications. This high-precision positioning is particularly important as piezo-positioners are increasingly used in high-speed applications like nano-storage of information and nanofabrication. Precision in positioning is lost during high-speed positioning due to motion-induced dynamic vibrations in the system. These vibrations can be compensated using inversion of the system-dynamics to find inputs that achieve exact output-tracking. Such an inversion-based approach finds the input that exactly tracks a desired output, but the resulting input may exceed available bandwidth or limits on available input-amplitudes. An optimal tracking approach is used in this paper to (a) optimize the positioning trajectory, and (b) restrict trajectory to the available bandwidth and saturation-limits of the amplifiers (used to apply voltage to the piezo-positioners). The approach is applied to the output tracking of a piezo-positioner and experimental results are presented.
1 Introduction
Piezo-positioners are used in scanning probe-based microscopy (SPM), which is a key enabling tool for nanotechnology. In addition to the use of SPM as a surface analysis tool, its potential for surface modification is now being exploited for nano-lithography. For example, SPM's have been used in both (a) additive techniques like localized chemical vapor deposition and (b) material removal techniques like localized etching of the surface with a gas or electrolyte (see for example, Gentili et al., 1993; Weck et al., 1997; Wiesendanger, 1994; Xie et al., 1997; and the references therein). A key advantage of such piezo-based nanofabrication is that it is the least expensive tool able to produce structures with dimensions below 100 nm. Piezo-positioners can also be used in the storage of information (Hosaka et al., 1997) and in the study of material and biological systems at the nano-scale (for a list of SPM applications see for example, Marrian, 1997; Regis, 1995; Vettiger et al., 1996; Wiesendanger, 1994). Thus, piezo-positioner based SPM's are poised to play a significant role in future technological progress, especially, when manufacturing processes in electronics, optics, and precision machining begin to require nanometer-scale control over features. However, a critical problem of current SPM-based (piezo-based) techniques is that they suffer from throughput-limitations, which are present in all serial-processing techniques -- the piezo-probe must visit each point where the surface analysis or modification is needed. This can take a prohibitive amount of time unless the positioning-speeds of piezo-based systems can be increased. The issue of high-speed optimal-positioning for piezo-based systems is studied in this paper.
The positioning bandwidth of piezo-based systems is limited by the lowest structural vibrational frequency of the system, because structural vibrations cause significant positioning errors (Pohl, 1986). For example, in scanning operations, turnaround transients can substantially limit the maximum scan-rates achieved (Barrett and Quate, 1991). These transients are proportional to the velocity changes (as in turnarounds) in the scan-path, and depend on the product of scan size and scan frequency -- thus any attempt to increase scan velocities increases the transients and thus decreases the useful part of the scan. Thus, the only choice with present approaches is to use piezo-positioners with fast dynamic response or to modify the dynamic response through feedback. Faster dynamic response can be achieved by using shorter piezo-tubes or piezo plate-scanners (Koops and Sawatzky, 1992), however, they tend to have limited positioning-ranges. An alternative approach is to improve the dynamic response by using feedback. For example, adding derivative feedback tends to suppress residual errors due to vibrations and thus allows faster scanning speeds. However, there are limits to the improvements achievable through feedback schemes and high feedback-gains tend to destabilize the system (Barrett and Quate, 1991). Further, feedback is not always available in piezo-based nano-positioning systems. To conclude, positioning bandwidth is significantly limited due to structural vibrations (when using standard feedback techniques).
Recent results have clearly demonstrated that significant improvements in positioning speed can be achieved by inverting the piezo-dynamics to find inputs that compensate for the structural vibrations (Croft et al., 1998b). Such inversion-based approaches have also been developed to account for hysteresis nonlinearities of the piezo-positioners when large range displacements are needed (Croft and Devasia, 1998a). The approach first linearizes the system dynamics by inverting the hysteresis nonlinearity, which is modeled as an input-nonlinearity. Second, the inversion-based approach is applied to the linearized piezo-dynamics to find exact output-tracking inputs. Although inversion-based approaches achieve exact tracking of the desired position-trajectory, a key issue is the design of the output position trajectory. For example, some output trajectories might require very large inputs to achieve exact-tracking -- such inputs might accelerate the depoling of the piezo-positioners. Further, the exact-tracking inputs found from inversion might exceed bandwidth limitations of the available piezo-amplifiers that apply the input voltages to the piezo-positioners. However, the exact-tracking inputs found from inversion are unique and therefore, the only recourse is to give up some of the exact-tracking requirement. Hence an optimal input is sought that trades the exact tracking requirement to achieve other goals like reduction of input-bandwidth and input-amplitudes. In this paper, a recently developed theory for optimal inversion (Dewey et al., 1998) is used to find optimal input voltages for piezo-positioners and experimental results are presented.
We begin with the formulation and solution of the general optimal-inversion problem in Section 2. In Section 3, we apply this technique to a piezo-probe and experimental results are presented. Our Conclusions are in Section 4.
2 Problem Formulation and Solution
In this section the output-tracking problem for
a general piezo-positioner is posed and solved in the frequency domain.
(MATLAB code to find the optimal inverse can be obtained by email to [email protected])
2.1 System Inversion for Exact Tracking
Let the dynamics of the piezo-positioner be described
by the following transfer function relationship in the frequency domain
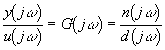
(1)
where u is the input and y is the
output. Given a desired output trajectory, yd , the inverse
input trajectory, ud , that achieves exact tracking can
be obtained by inverting the system's dynamics (Equation 1) to obtain (Bayo,
1987)
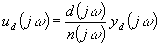
(2)
2.2 The Performance Criterion
The exact-output tracking input, found from Equation 2, is "unique" (Bayo, 1987; Devasia et al., 1996; Ledesma et al., 1994). For a generic desired output trajectory, this exact tracking input might be large and therefore depolarize the piezo-positioner or saturate the piezo-amplifiers. The input might also excite unwanted resonance's in the piezo-positioner and in the structure that houses the piezo-positioner. The input-bandwidth needed to achieve this positioning trajectory may not be available through the piezo-amplifier. Therefore, the goal of the optimal inverse is to generate a modified output trajectory as well as to find the input needed to achieve tracking of this new trajectory. Note that desired output trajectories are typically chosen in an ad-hoc manner. For example, the output is typically chosen as triangular to-and-fro scans, in scanning probe microscopy. It has been shown that these triangular scans cannot be tracked exactly, because the velocities are discontinuous at the corners leading to infinite accelerations. Therefore, the corners have to be smoothed to achieve exact tracking (Tamer and Dahleh, 1994). Our approach generalizes the "smoothing process". We formulate the optimal trajectory redesign problem as the minimization (over all possible inputs, u) of a quadratic cost functional of the type

(3)
where the superscript * denotes complex conjugate transpose. In this optimization criterion, R(jw ) and Q(jw ) are non-negative frequency-dependent real-valued scalars that represent the weights on control-input, and the output-tracking-error, respectively, and yd is a desired output-trajectory (for requirements on yd , see Bayo, 1987; Devasia et al., 1996). The weights, R(jw ) and Q(jw ), should not be both simultaneously zero at any frequency.
2.3 Optimal Input
Our main result is given by the following lemma, which finds the optimal input trajectory. A generic result for linear multi-input multi-output systems can be found in Dewey et al., 1998. Lemma The optimal inverse input trajectory uopt, is given by

(4)
The optimal modified output trajectory is given
by

(5)
Proof:
The cost functional (Equation 3) can be rewritten
as (see Lemma in reference Dewey et al., 1998 for a similar argument)
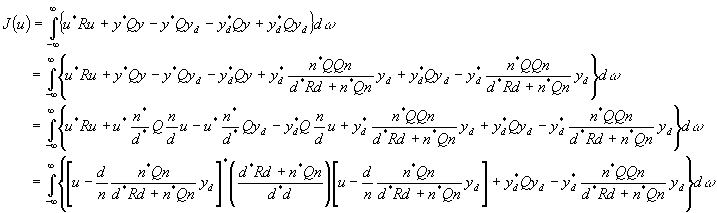
(6)
where the explicit dependence on jw
is not written for ease in notation and the superscript * implies complex
conjugate. Note that the only term with u inside the integral is
quadratic in u and hence the Lemma follows by setting this quadratic
term to zero.
Remark 1
We point out two extreme cases. First case: if
the weight on the tracking error is zero, Q=0, but R is positive
definite then the optimal input is uopt=0, i.e., the
best strategy is not to track the desired trajectory at all. Second case:
if the weight on the inputs are zero, i.e., R=0 but with Q
positive definite then yopt= yd. This implies
that exact output-tracking is optimal, and the cost is again zero. The
resulting optimal inverse is the exact-inverse input that achieves exact
tracking of the prescribed output, yd , without any modification.
Remark 2
Frequency dependent weights (R and Q)
on the input and output-error can be used, for example, to account for
actuator-bandwidth-limitations (Gupta, 1980).
This is illustrated with experimental results in the following section.
3 Experimental Verification
In this section the experimental system is described,
and experimental results are presented and discussed.
3.1 Modeling of the Experimental System
The experimental piezo-positioning system (see
Figure 1) consisted of a sectored piezo-actuator that was used for lateral
displacement and an inductive sensor that measured this lateral displacement.
The lateral motion of the sectored piezo-actuator was achieved by applying
voltages across opposite electrodes of the sectored piezo-actuator. The
complete experimental system also included amplifiers for the piezo-actuator
and the electronics needed to condition the sensor outputs.
Figure 1: Experimental Piezo-positioning
System
The piezo-system was modeled as a cascade of
two subsystems. The first subsystem modeled the hysteresis nonlinearity,
and the second subsystem modeled the structural dynamics of the piezo-positioning
system. The hysteresis nonlinearity was determined by applying a triangular
shaped voltage profile to the system at low frequency (1 Hz) and measuring
the input-output response. Note that at low input frequencies (relative
the first resonant frequency of the piezo-positioning system), structural
vibrations have little effect and can be neglected. An inverse hysteresis
model for the resulting input-output hysteresis response was then modeled
as separate third order polynomials for increasing or decreasing voltage
profiles (see Croft and Devasia, 1998b).
The linear structural model was determined next, using a Dynamic Signal
Analyzer (HP3650A). As shown in Figure 2, the command from the signal analyzer
was passed through the inverse hysteresis model (implemented using a personal
computer) and the resulting signal was sent to the experimental piezo-system.
The measured signal from the inductive sensor was then returned to the
signal analyzer. The resulting input-output response, measured from the
signal analyzer, was used to model the structural dynamics of the system.
The Bode plot, found experimentally from the signal analyzer, is given
in Figure 3
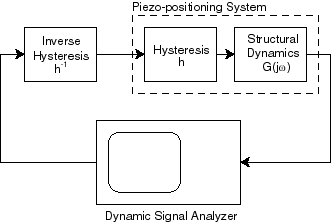
Figure 2: Determination of the Structural Dynamics of the Experimental Piezo-positioning system
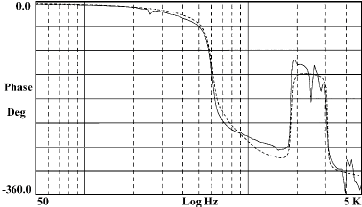
Figure 3: Bode plots of experimental system. The model captures the system behavior up to the first fundamental vibrational frequency of 600 Hz. (Solid Line: Experimental Dashed Line: Model)
The resulting transfer function (model) from
the signal analyzer can be written as

(7)
where y is the output measured from the inductive
sensor (in volts) and u is the voltage applied to the piezo-positioning
system. The parameters for the experimental piezo-positioning system were:
k = .454; a = -1.93x104; b= -1.61x108; c = -2.75x1012;
d = -3.87x1016; e = 5.62x103; f = 4.28x108;
g = 2.08x1012; h = 1.80x1016; i = 3.13x1019;
and m = 1.64x1023. This linear model then can be inverted by
using equation (2) to find the inverse input trajectory. The optimal inverse
input trajectory can be found using equation (4).
3.2 Results
Three sets of experiments were performed: (1)
output tracking without using information about the system's dynamics,
i.e. applying yd divided by the direct current (DC) gain
of the system (2) using the inverse input trajectory without frequency
weighting (i.e. R=0 for all frequencies) and (3) using the inverse
input trajectory with optimal frequency weightings for R(jw
) and Q(jw
) as given in Table 1 (the values of
R(jw
) and Q(jw
) at other frequencies were obtained
by linearly interpolating between the specified values). Plots for the
response of the piezo-positioning system for these three cases are given
in Figures 4-7. The applied voltage profiles for select scanning frequencies
for cases (2) and (3) are given in Figure 8.
Frequency, w
(Hz)
|
0.0
|
550
|
650
|
100000
|
R(jw
)
|
0.0
|
0.0
|
.02
|
.02
|
Q(jw
)
|
1.0
|
1.0
|
1.0
|
1.0
|
Table 1: Frequency Weighting
It is noted that the desired output trajectory (displacement trajectory)
was chosen as a back and forth scanning (triangular shaped) of the piezo-positioning
system (see, for example, Croft and Devasia, 1998a).
3.3 Discussion of results
As shown in Figure 4, scan path tracking without
considering the system dynamics (i.e., using inputs that only use information
about the DC gain factor) can only achieve good tracking at low scan
rates, such as 25 Hz. However as the scan rate increases, structural vibrations
of the piezo-positioning system adversely affect the tracking performance
of the piezo-positioning system. By the 75 Hz scan rate, these vibrations
have become substantial and scan path tracking is poor.
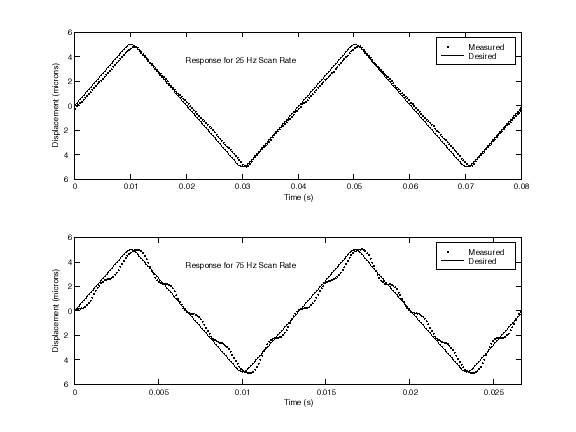
Figure 4: Scan path tracking for yd divided by the DC gain of the system only. Scan path tracking is achieved for a 25 Hz scan rate but structural vibrations cause loss of tracking for higher scan rates such as the 75 Hz scan rate.
In contrast, Figure 5, shows that the tracking
of the system for the inverse input without optimal frequency weighting
(R = 0), improved at the 75 Hz scan rate (compare with Figure
4). However, as the scan rate increases further, the tracking of the system
degrades due to the unmodeled frequency content in the feed-forward applied
voltages required to achieve the scan path. For example, Figure 5 shows
that the 150 Hz scan path tracking was poor due to this unmodeled frequency
content in the feed-forward applied voltages.
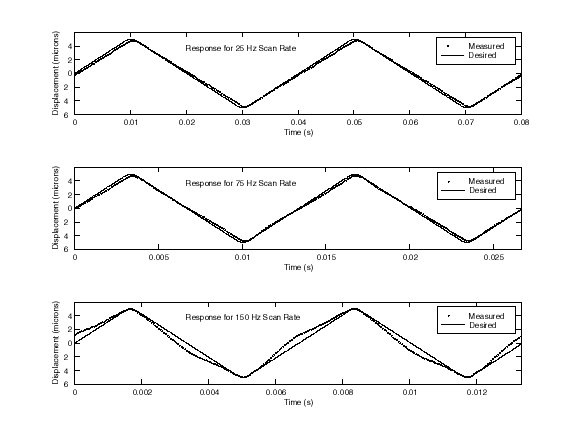
Figure 5: Scan path tracking for the inverse input trajectory without optimal frequency weighting. The inverse input trajectory substantially improves the 75 Hz scan rate (compare with Figure 4), but fails to sufficiently track at higher frequencies (such as 150 Hz) due to the unmodeled frequency content in the input signal.
At the lower scanning frequencies, the addition
of optimal frequency weighting to the inverse input trajectory, achieved
scan path tracking comparable to the scan path tracking achieved by the
inverse input trajectory without optimal frequency weighting (compare the
results in Figure 6 with those in Figure 5). Furthermore, with the addition
of the optimal frequency weighting to the inverse input trajectory at higher
frequencies, scan path tracking was greatly improved. The scan path tracking
at 150 Hz improved substantially and the scan path tracking was extended
to higher scan rates, such as 350 Hz (see Figures 6 and 7). This improved
tracking is due to the removal of the higher unmodeled frequency content
in the feed-forward input. It is also noted that the high-frequency content
in the input (seen in Figure 8) corresponds to the zero-frequency in the
system dynamics close to 2000 Hz (see the dip in the Bode Plot in Figure
3). The corresponding high-amplitude inputs near the zero-frequencies,
have relatively low impact on the desired output and are removed in the
optimal inversion process. However, when the higher frequency content of
the scan signal is filtered out, the resulting scan path is "smoothed"
at the corners due to the loss of the higher frequency components of the
feed-forward voltage. The effects of this can be seen in the 150 Hz and
350 Hz scan rate of Figure 7.
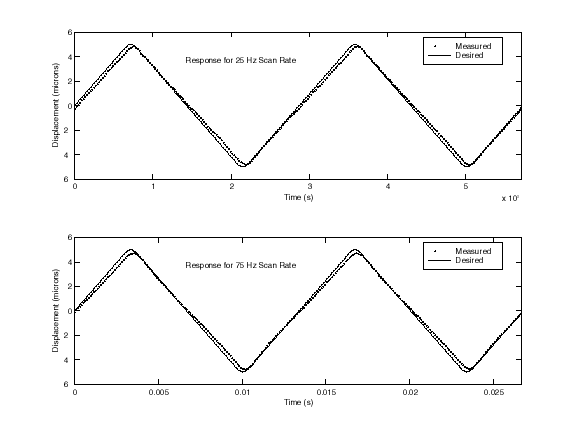
Figure 6: Scan path tracking for inverse input trajectory with optimal frequency weighting. The addition of optimal frequency weighting to the inverse input trajectory achieves scan path tracking comparable to the scan path tracking achieved by the inverse input trajectory without optimal frequency weighting (compare the results in Figure 6 with those in Figure 5).
Figure 7: Scan path tracking for vibration compensation with optimal frequency weighting. The addition of optimal frequency weighting to the inverse input trajectory substantially improves scan path tracking at the 150 Hz scan rate (compare with Figure 5). Higher scan rates (350 Hz) are also achieved with some "smoothing" of the corners of the scan path.
The applied feed-forward voltages for the inverse input trajectory without optimal frequency weighting and the inverse input trajectory with optimal frequency weighting are compared in Figure 8. At the lower scan rate of 75 Hz, there was little difference between the applied feed-forward voltages. At the higher scan rate of 150 Hz, the applied feed-forward voltages are significantly different. The high frequency components have been removed from the optimal inverse input (compare the inverse input and the optimal inverse input for the 150 Hz scan rate) which leads to improved tracking for the optimal inverse case. At even higher scan rates (350 Hz), the applied voltage for the inverse input becomes large compared to the applied voltage for the optimal inverse input (at 350 Hz). Note that these inputs are also trying to force tracking at bandwidths where the modeling is relatively poor, resulting in poor tracking. In contrast, the optimal inverse input is smaller and achieves better tracking.
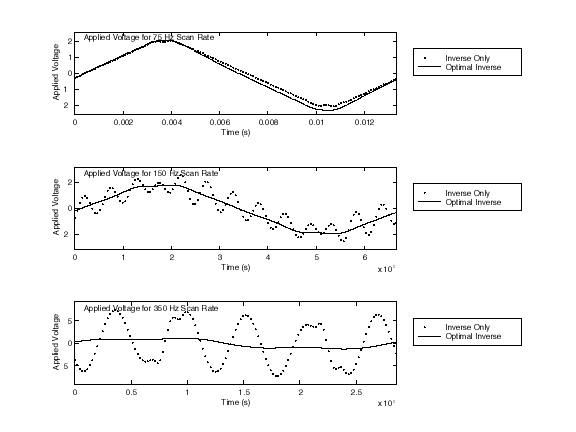
Figure 8: Applied voltages to piezo-positioning system. The addition of optimal frequency weighting to the inverse input trajectory removes the high frequency components (see 150 Hz and 350 Hz scan rate) and reduces the amplitude (see 350 Hz scan rate) of the applied voltage profiles.
4 Conclusions
The optimal inversion-based approach is used
to successfully exploit the known piezo-dynamics and optimally modify the
desired position trajectory. The approach provides a systematic method
to an optimal tradeoff between tracking the desired trajectory and other
goals like vibration reduction or reduction of required inputs. The approach
demonstrated a substantial increase in the effective bandwidth of
the experimental piezo-positioning system (more than an order of magnitude
increase, from 25 Hz scanning rate for the output tracking without using
information about the system's dynamics, to 350 Hz scanning rate when using
the optimal inverse input).
5 References
-
Barrett, R. C. and Quate, C. F. (1991) Rev. Sci.
Instrument., 62 No. 6, June, pages1393-1399, Optical scan-correction system
applied to atomic force microscopy
-
Bayo, E. (1987) J. of Robotic Systems, 4 No.1, pages
63-75, A finite-element approach to control the end-point of a single-link
flexible robot
-
Croft, D. and Devasia, S. (1998a) AIAA Journal of
Guidance, Control, and Dynamics, 21 No. 5, Sept.-Oct., pages 710-717, Hysteresis
and vibration compensation for piezoactuators
-
Croft, D.; McAllister, D.; and Devasia, S. (1998b)
ASME Journal of ManufacturingScience and Engineering, 120 No. 3, August,
pages 617-622, High-speed scanning of piezo-actuators for nanofabrication
-
Devasia, S.; Chen, D.; and Paden, B. (1996) IEEE
Transactions on Automatic Control, 41 No. 7, pages 930-943, Nonlinear inversion-based
output tracking
-
Dewey, J. S.; Leang, K.; and Devasia, S. (1998)
ASME Journal of Dynamic Systems, Measurement and Control, Scheduled to
Appear in December 1998, Experimental and theoretical results in output
trajectory redesign for flexible structures
-
Gentili, M.; Giovannella, C.; and Selci, S., editors
(1993) Nanolithography: A Boderland between STM, EB, IB, and X-ray Lithographies,
NATO ASI Series E: Applied Science, 264, Kluwer Academic Publishers
-
Gupta, N. K. (1980) Journal of Guidance and Control,
3 No. 6, November, pages 529-535, Frequency shaped cost functions: Extension
of linear-quadratic-gaussian design methods
-
Hosaka, S.; Kikukawa, A.; Koyanagi, H.; Shintani,
T.; Miyamoto, M.; Nakamura, K.; and Etoh, K. (1997) Nanotechnology: Special
issue on Scanning Probe-based Nanoelectronics, 8 No. 3A, September, pages
A58-A62, SPM-based data storage for ultrahigh density recording
-
Koops, R. and Sawatzky, G. A. (1992) Rev. Sci. Instrument.,
63 No. 8, August, pages 4008-4009, New scanning device for scanning tunneling
microscope applications
-
Ledesma, R.; Devasia, S.; and Bayo, E. (1994) Journal
of Robotic Systems, 11 No. 4, pages 327-338, Inverse dynamics of spatial
open-chain flexible manipulators with lumped and distributed actuators
-
Marrian, C. R. K., editor (1997) Special Issue on
Nanometer-scale Science and Technology in the Proceedings of the IEEE,
85 No. 4, April
-
Pohl, D. W. (1986) IBM J. Res. Dev., 30 No. 4, July,
pages 417-427, Some Design Criteria in Scanning Tunneling microscopy
-
Regis, E., editor (1995) Nano, Little, Brown and
Company
-
Tamer, N. and Dahleh, M. (1994) Proceedings of Control
and Decision Conference, Lake Buena Vista, Florida, pages 1826-1831, Feedback
control of piezoelectric tube scanners
-
Vettiger, P.; Staufer, U.; and Kern, D.P., editors
(1996) Special Issue on Nanotechnology in Journal of Microelectronic Engineering,
32, Elsevier, New York
-
Weck, M.; Fischer, S.; and Vos, M. (1997) Nanotechnology
, 8 No. 3, September, pages 145-148. Fabrication of microcomponents using
ultraprecision machine tools
-
Wiesendanger, R., editor (1994) Scanning Probe Microscopy
and Spectroscopy, Cambridge University Press
-
Xie, W.; Dai, X.; Xu, L. S.; Allee, D. A.; and Spector,
J. (1997) Nanotechnology, 8 No. 2, June, pages 88-93, Fabrication of Cr
nanostructures with scanning tunnelling microscopes
|